Before the 1970s, clay bricks and high alumina bricks were mainly used as refractory materials for heating furnaces in China, and the furnace structure was mainly a dome structure. Due to the use of low-grade refractory materials with poor high-temperature performance, coupled with defects in the furnace structure, the service life of the heating furnace is very low. In addition, the furnace top bricks are prone to looseness, detachment, and rapid local damage during operation, resulting in frequent maintenance and low operation rate of the heating furnace.
During the late 1970s to 1980s, ramming materials, plasticizers, clay castables, and cement-based ordinary castables began to be used on heating furnaces. The application of the above materials in heating furnaces has changed the traditional brick furnace structure and started the application period of amorphous refractory materials in heating furnaces. The furnace structure constructed using ramming materials, plastic, clay castables, and cement combined with ordinary castables can not only adopt a flat top structure for easy masonry, but also have good overall integrity and air tightness, which is conducive to the operation and maintenance of the heating furnace.
In the late 1980s, with the continuous advancement of amorphous refractory material technology, a series of high-tech refractory materials such as low cement, ultra-low cement, and cementless castables were introduced in China and applied in various thermal kilns in the metallurgical industry. Low cement, ultra-low cement, and cementless castables are a type of high-tech refractory castables developed on the basis of ordinary castables using rheological principles, closest packing theory, and finer powder technology. Due to the use of the closest packing theory and ultrafine powder technology, this type of material has the characteristics of low porosity, small pore size, high density, good volume stability, high strength, and low water addition.
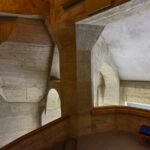